Author: Piotr Grudzień, Innovation Consultant at Bax & Company
The picturesque mountainous region of Grenoble in France is the epicentre of TES’ battery recycling efforts, a critical component in the company’s suite of technology lifecycle management services. Originally founded in 1998 as Recupyl, the spin-off from the University of Grenoble developed an industry-leading battery recycling process serving global customers. Today, this pioneering solution is closing the loop on electric vehicle (EV) batteries around the world.
Business sustainability is an important consideration and the company’s operations have a very low impact on their local environment in terms of emissions to air, soil and water. Furthermore, the inherent low energy consumption adds to the environmental benefits of this unique patented process. BatteReverse partner TES, a global technology lifecycle management company with a commitment to ‘sustaining tomorrow’, acquired Recupyl in 2018.
The Singapore-based company provided the resources and capital required to scale up processes based on IP developed in Grenoble and build new plants capable of processing growing volumes of EV batteries. TES has a vision to deliver integrated IT lifecycle solutions and enable clients to manage the inherent complexities and risks associated with battery packs in the technology and electric vehicle (EV) markets. Developing new, proprietary technologies and patents for hydrometallurgical processes, TES has evolved quickly and innovated to establish itself at the forefront of the battery recycling industry.
The expertise gained in France has played a key role in TES opening South-East Asia’s first battery recycling facility in 2021 (working with a double closed loop: water process reuse as well as cobalt output reused as a precursor for battery materials) and commissioning a new, large-scale mechanical and hydrometallurgical plant here in Europe. We visited the site in Grenoble and met Dr. Farouk Tedjar, Innovation Director at TES and the R&D team, to find out more about the company’s business model and shed some light on the current challenges and development opportunities in the recycling of EV batteries.
What happens at the recycling facility in Grenoble?
Let’s break down the recycling process of an EV battery pack at the TES facility. First, the battery pack is removed from the packaging and discharged for safety reasons. Then, the pack is manually opened, and modules are extracted. The remaining battery pack components (casing, cables, electronics, cooling system) are sorted and recycled via TES’s network of global recycling facilities. All modules are assessed for reuse potential if the State of Health (SoH) is sufficiently high.
Any remaining modules are further discharged and segregated to be recycled. Using proprietary in-house technology auto-punching machines and shredders break the end-of-life batteries down into fine substances. Environmental, health and safety considerations are vital, so this process is carried out in an inert atmosphere, reducing the risk of thermal runaway accidents and preventing the release of secondary contaminants like heavy metals or volatile organic compounds into the atmosphere.
The small pieces are separated using screens and fractions are divided into steel, plastics and active materials in the form of a black mass. Steel and plastics are recycled within Europe and part of the remaining black mass is transported to TES’s approved and compliant downstream partners until the TES facility is opened in Rotterdam. The site in Grenoble has the capacity to handle 14 tons of lithium-ion batteries per day with over 90% recovery rates. Cobalt and lithium are recovered with up to 99% purity, standards so high they can be purified for reuse in the production of new batteries.
What sets the Grenoble site apart from other operations within Europe is the bespoke, low-powered, patented process that can give a second life to a broad range of valued materials. Through leaching and precipitation, a proprietary hydrometallurgical reactor converts the black mass into secondary raw materials including graphite, cobalt, nickel and manganese. These materials are sold into the battery supply chain of OEMs or manufacturers of lower-value products.
The business model– an established recycler evolving to meet growing demand
Even the most advanced technologies cannot work without a solid business model. This business model is based on many years of experience extending the usable life of technology assets, parts, and commodity materials for global customers. TES provides an end-to-end recycling service including the management of shipping, reverse logistics and environmental compliance.
TES operates a service-lead business model with additional value recovery opportunities. Customers pay for recycling services providing a forecastable income stream. Revenues are supplemented with value returns from recovered parts and recycled materials which are shared with larger, strategic clients.
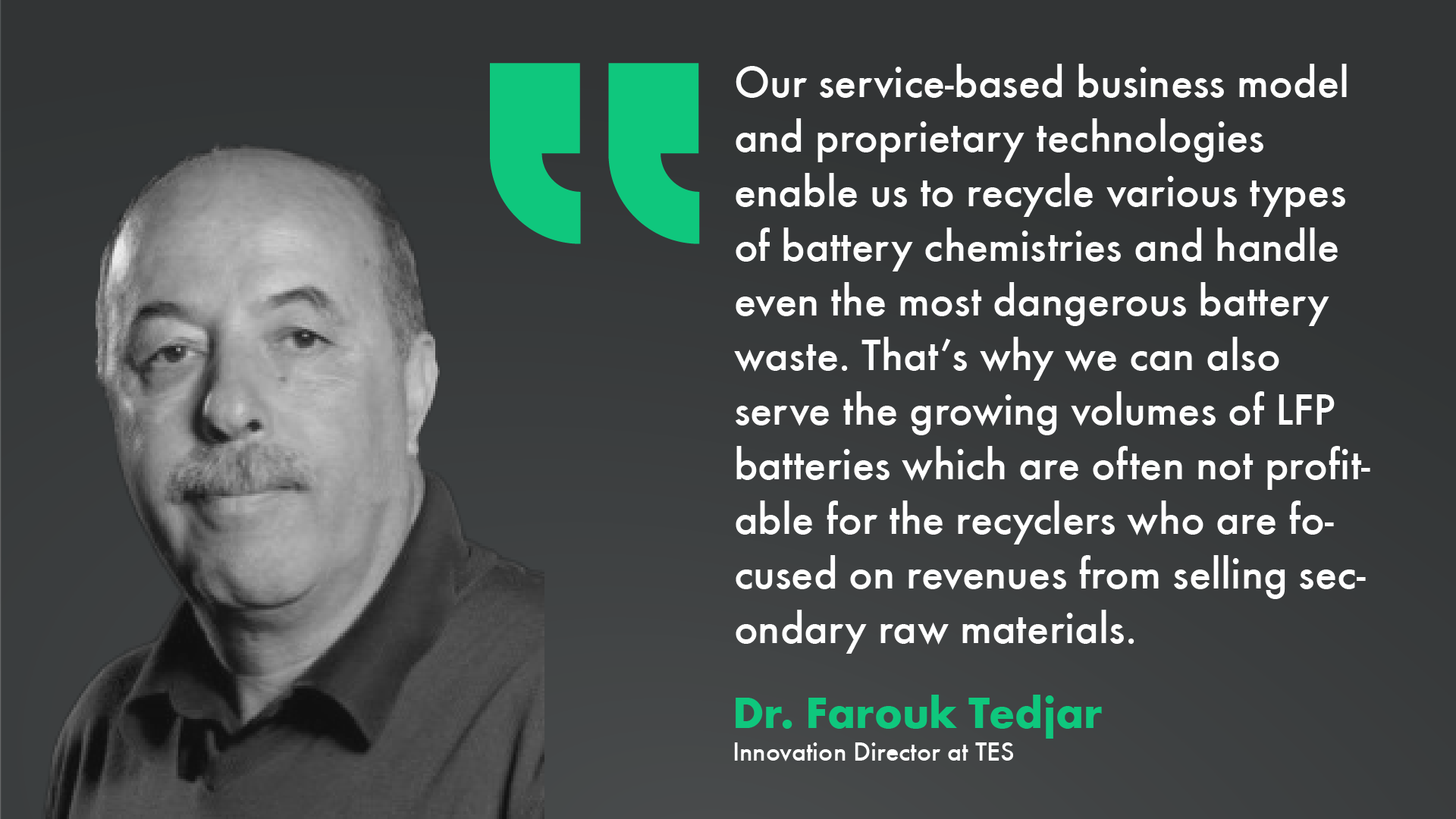
Originally founded by Dr Farouk Tedjar as Recupyl developed its recycling capabilities to exceed current and future regulatory requirements, particularly minimum recycling rates. Focusing on batteries containing scarce metals like nickel, cobalt and lithium, initially, the predominant customers were collection schemes of portable batteries. Today TES works directly with EV OEMs and cell manufacturers (so called “Gigafactories”).
Some of the automotive manufacturers have specific requirements including dismantling high voltage charging connectors before recycling so that they can be reused by the manufacturer. Thanks to the flexibility and extensive experience of the staff, TES can develop solutions for bespoke client requirements, giving them a reputation as the recycling ‘special task force’ among their established clients.
After 35 years of operation, the company serves many global customers and continues to develop new recycling technologies. R&D costs are covered largely through EU-funded collaborative projects, such as MARBEL, RHINOCEROS, and of course, BatteReverse.
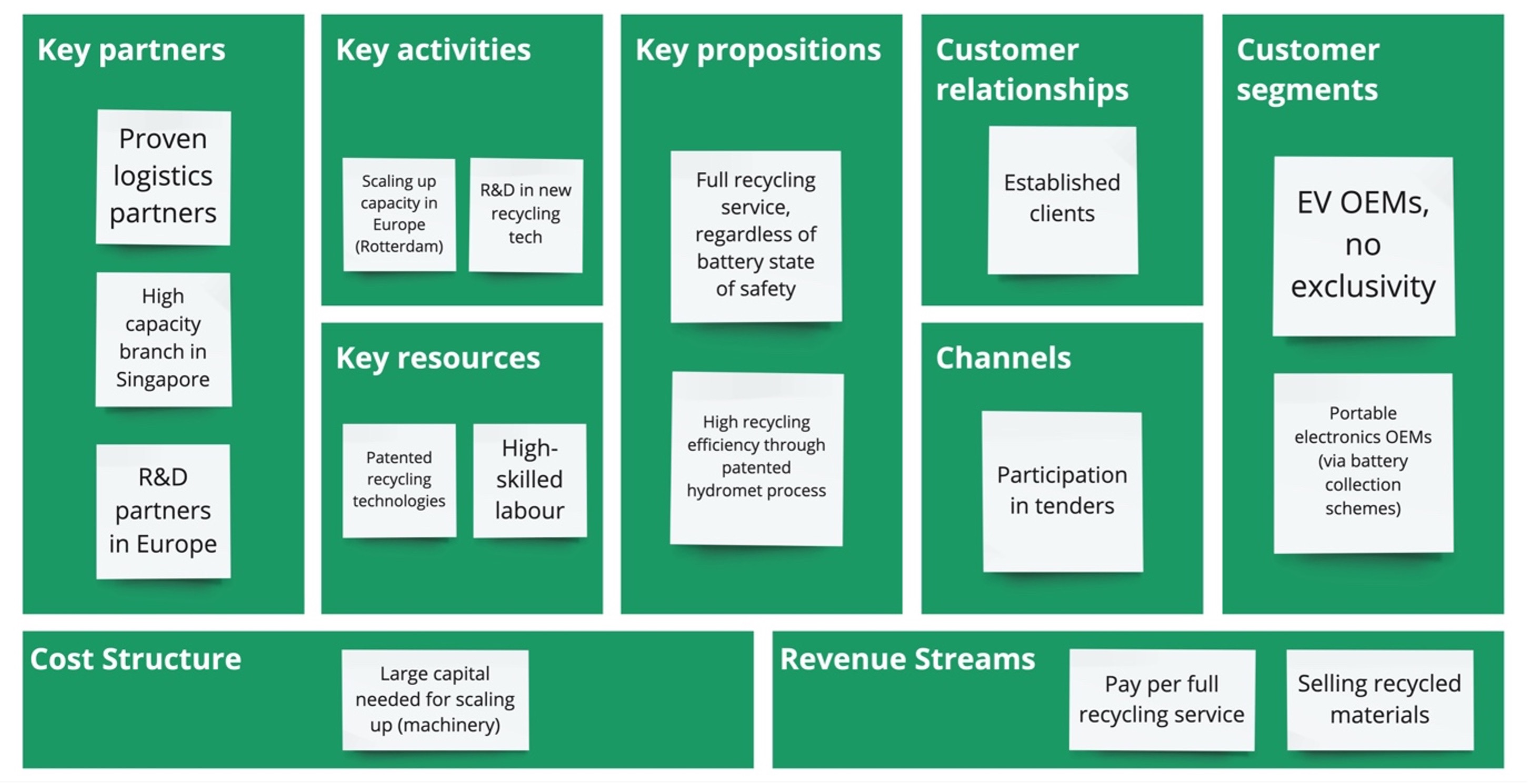
Key challenges for efficient recycling of EV batteries
TES has circularity at its core and is focused on sustaining tomorrow. The company is a key enabler for EV OEMs to improve the sustainability of their business models. With ongoing growth and change in the EV marketplace, the team at TES know that they need to evolve, innovate, and lead. There are opportunities to improve the circularity of materials within the EV business model which will be achieved by working in partnership with stakeholders throughout the EV supply chain.
The dismantling process is currently inefficient due to the use of adhesives in new batteries. It is difficult and not economical to dismantle the EV battery modules to the cell level, which limits the number of components that can be reused - lowering the recycling efficiency. Another barrier is the complexity of the components and the large variety of battery types, requiring a manual dismantling process and preventing opportunities for automation.
On the business side, the volatility of prices for battery-grade secondary raw materials (cobalt, nickel, lithium) destabilises the operation of recyclers who focus only on popular NMC chemistry and don’t want to recycle chemistries with low materials value, such as LFP. While these recyclers may currently be more profitable and easier to scale up, the dynamic battery market may deem some new investments unprofitable in the long term.
Finally, economies and scale and logistics. Some of the black mass produced in Grenoble is currently transported overseas, mainly because there is currently no large-scale hydrometallurgical recycling capacity in Europe.
Scaling up hydrometallurgical recycling in Europe
TES is addressing some of these challenges by setting up a new recycling facility at the Port of Rotterdam with an annual capacity of 10,000 tonnes of batteries and an initial footprint of 10,000 m2. This plant, the first battery recycling facility in the Netherlands, will combine the technologies developed in Grenoble, and experience from operating the large-scale recycling plant in Singapore. The strategic location of the facility right in the port will allow for improved logistics of the input (end-of-life batteries) and output (black mass and secondary raw materials) bringing the much-needed capacity to complete the European battery circularity value chain.
The combined capacities of the three facilities will not only make TES one of the largest recycling providers but also the largest generate of commercial grade materials produced from the process, supporting the manufacturing of new batteries and reducing over-consumption of resources and reliance on unsustainable supply chains.
With BatteReverse, TES is going to pilot a novel safe and efficient method of opening EV battery packs which should significantly reduce the time needed for dismantling and improve the profitability of recycling overall.
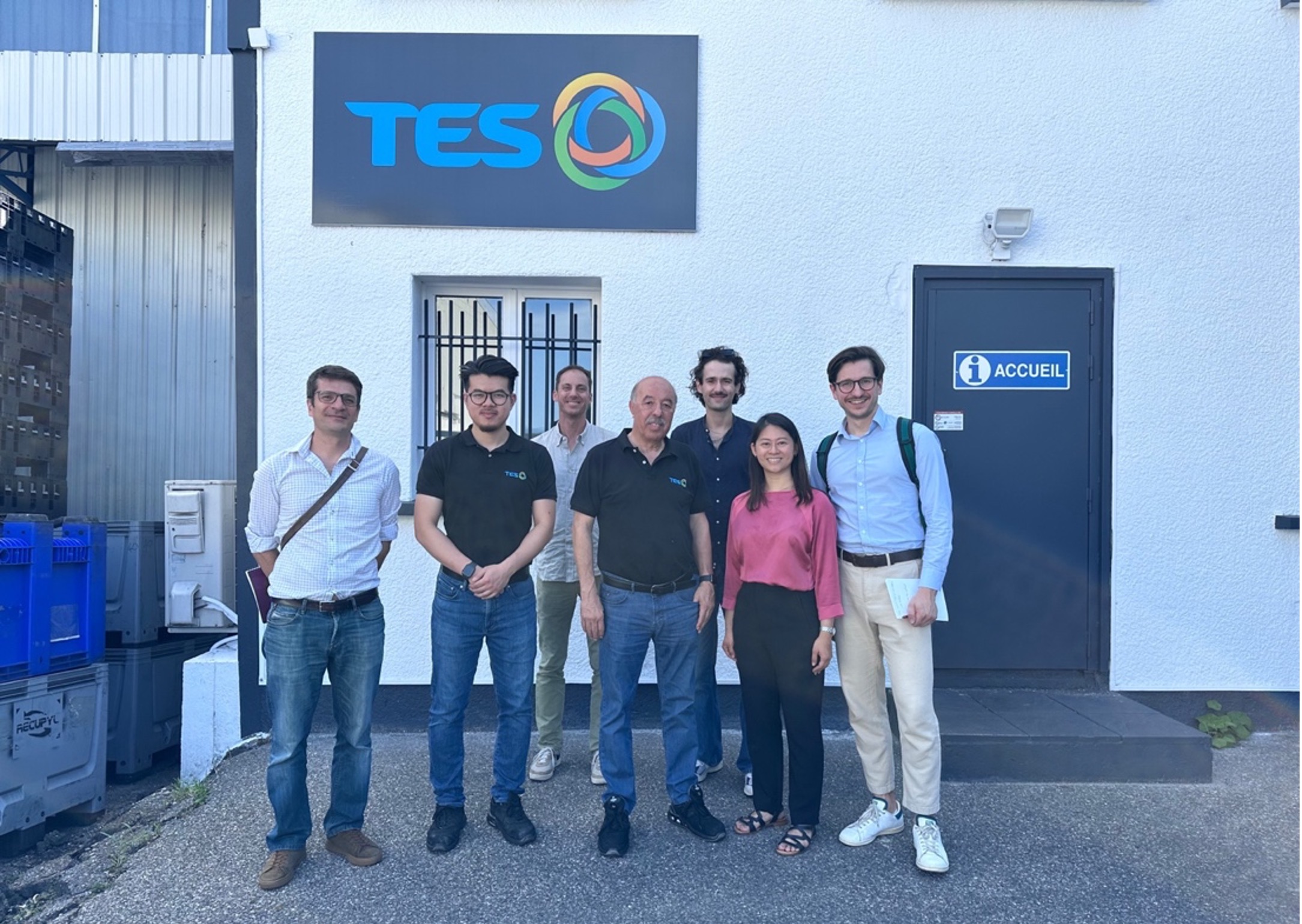
This case study was elaborated as part of the BatteReverse project by Bax & Company with input from TES. The article is part of the Circular Business Cases series, which analyses existing business models for Li-ion batteries.
Join the BatteReverse community for more industry insights shaping the battery circularity landscape.
About TES
Since its formation in 2005, TES has grown to become a global leader in sustainable technology services and bespoke solutions that help clients manage the commissioning, deployment, and retirement of technology devices and components. TES provides comprehensive services for technology devices throughout their lifecycle - from deployment to decommissioning to disposition - all the way through to recycling and end-of-life repurposing. This includes innovating new processes to leverage the value locked in assets if they are to be recycled, such as our proprietary lithium battery recycling process, which extracts scarce materials from used batteries at purity rates high enough that they can be reused in the manufacturing supply chain.
TES has made it its mission to make a decade of difference by securely, safely, and sustainably transforming and repurposing one billion kgs of assets by 2030. The company’s 40 owned facilities across 22 countries offer unmatched service-level consistency, consistent commercials, lower logistics costs, local compliance experts in-region, support in local time zones and languages, and a deep understanding of transboundary movement globally.
For more information, visit www.tes-amm.com.